6 min read
Top 5 Challenges in Raw Wood Volume Logistics
ConiferSoft Communication Department | December 26, 2024
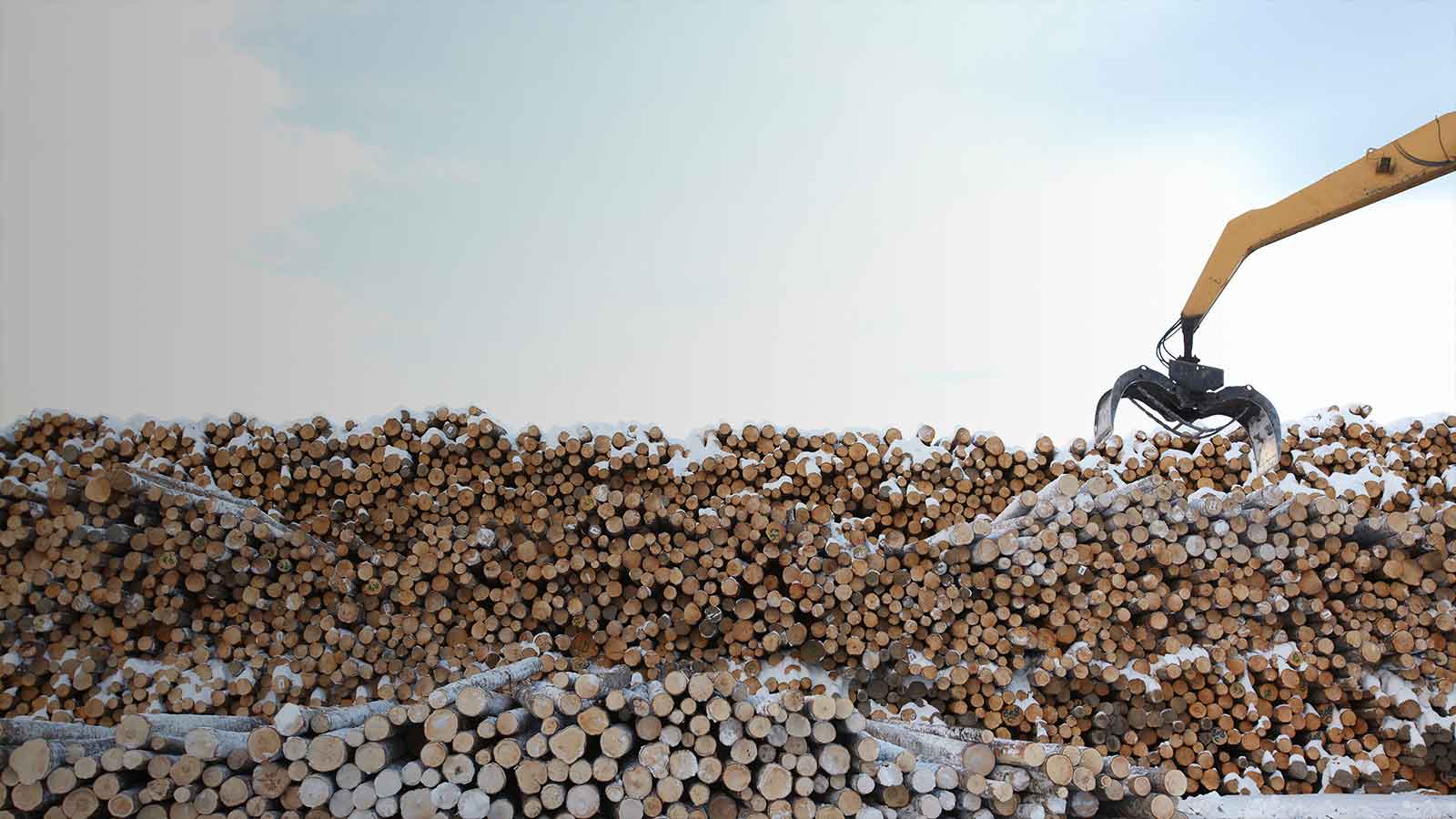
Managing wood logistics in mill yard isn't just about moving wood from point A to point B. It involves a series of complex challenges that can affect both budgets and overall performance. The intricacies of coordinating transportation, meeting compliance standards, managing unpredictable inventory, and maintaining efficient storage can lead to complications that drive up operational costs and slow down logistics.
The consequences of these challenges are far-reaching. They can disrupt production timelines, incur unexpected expenses, and complicate relationships with both suppliers and customers. In an industry where precision and timing are critical, even small inefficiencies can have a disproportionate impact on the bottom line. Unpacking these issues is the first step to identifying how to navigate them more effectively.
1. Rising Transportation Costs and Infrastructure Limitations
Transportation is one of the largest cost factors in wood logistics. Wood raw materials are often heavy, bulky, and difficult to move, frequently requiring specialized trucks. The particular transport needs alone add to the cost. However, the real challenge goes beyond just the logistics of moving the wood material—it’s about the infrastructure in place to support these operations.
Many rural logging areas are poorly connected to major highways or rail networks, with infrastructure that cannot support wood truck traffic. As a result, transportation routes may be suboptimal, extending the distance traveled and increasing fuel and maintenance costs. Furthermore, as fuel prices fluctuate and vehicle maintenance becomes more expensive, transportation costs can quickly spiral out of control.
Without careful route planning and regular maintenance management, these inefficiencies can accumulate and affect profitability.
Solution
To reduce transportation costs and improve logistics, businesses need to focus on optimizing transport routes and managing their operations more effectively. By analyzing routes, companies can identify the most cost-efficient paths, minimizing fuel consumption and travel time. In addition to optimizing routes, effective vehicle management ensures that trucks are well-maintained, reducing the risk of costly breakdowns and repairs. Cutting unnecessary trips and eliminating empty runs also helps lower costs and enhance overall logistics efficiency.
LogDrive is a modern supply chain solution designed to optimize the transport of raw materials from the forest to production sites by streamlining transport orders. It digitizes the process, reducing manual tasks and paper handling, which lowers the risk of errors and improves coordination between stakeholders. By offering precise routing instructions and using truck and lorry load data, LogDrive helps minimize fuel consumption and reduce costs. Orders are clearly visible on color-coded maps for easy understanding, and essential details auto-populate to simplify reporting and verification.
Designed specifically for forest logistics, LogDrive enhances delivery efficiency and ensures smoother, more reliable transportation of raw materials.
2. Environmental and Regulatory Compliance
The regulatory landscape for the forestry industry has seen significant changes in recent years, as countries and regions introduce more stringent laws to protect forests and promote sustainable practices. A particularly pressing consideration is compliance with the EU Deforestation Regulation (EUDR) that is mandated to go into effect by December 2025, which requires companies to verify that the wood they source is not linked to deforested land.
For businesses handling raw wood materials, this means tracking every wood’s origin and verifying its compliance throughout the supply chain. Ensuring compliance with such regulations is no small feat, particularly as businesses may be dealing with pulp wood sourced from multiple regions or countries, each with its own set of laws and sustainability standards. Failing to comply can result in fines, loss of market access, and reputational damage.
The complexity grows when companies need to manage multiple certifications and environmental standards, all while keeping up with changes in legislation and ensuring full traceability across the supply chain.
Solution
To effectively manage regulatory compliance, companies need proper tracking and documentation systems that ensure full traceability of wood from its source to final delivery. This involves maintaining a complete record of the origin and sustainability of all wood products handled, as well as monitoring the environmental impacts of their logistics processes.
YardManager is an innovative solution for pulp and recycled paper mills that provides real-time tracking and traceability of wood or pulp bales from entry to processing, ensuring compliance with regulations like the EUDR. Offering accurate insights into wood or pulp bales origin and sustainability, YardManager also minimizes errors, reduces material losses, and improves inventory management. Unlike manual tracking systems, such as Excel, which often causes inaccuracies, YardManager streamlines operations with up-to-date stock data. This enables mills to integrate regulatory compliance seamlessly into daily operations, helping avoid fines, shutdowns, and reputational damage while optimizing processes.
For companies involved in biofuels or heating plants, BioBiz provides significant control over the biofuel supply chain, from procurement to delivery, ensuring traceability to meet regulation standards such as EUDR requirements. It offers real-time insights into delivery volumes and quality, allowing heating plants to track and verify biofuel sources with precision. By automating tasks like invoice verification and inventory reconciliations, BioBiz reduces manual errors and simplifies compliance through its digital approach, providing clear documentation and full transparency across the supply chain.
3. Efficient Storage and Management of Wood
Storing raw materials like pulp wood is far more complex than simply stacking them. These materials requires specialized storage strategies to preserve wood quality. Improper storage can lead to degradation, pest infestations, or rot, resulting in significant financial losses.
A disorganized mill yard can also create inefficiencies, such as wasted time searching for specific materials. This not only increases labor costs but also reduces overall operational efficiency, especially as the volume of raw materials grows. Proper storage management is critical to maintaining productivity and preventing avoidable costs.
Additionally, with the increasing volume of wood being managed, it can become very challenging to track everything manually, leading to errors or confusion.
Solution
Efficient storage and handling come down to organization. Businesses must categorize wood based on size, quality, type, and intended use. As material volume grows, manual tracking becomes inefficient and error-prone. Implementing an automated system to track wood and monitor yard movements can make storage handling more efficient.
YardManager is designed to streamline wood handling. By providing real-time visibility into raw material feed to debarkers, it ensures a consistent mix and facilitates predictive assessments of chip quality. The system offers up-to-date information on grade, volume, and location.
Log stacker drivers benefit from dynamic, real-time maps showing the location of wood for active production orders, optimizing movement and reducing inefficiencies. All raw material movements in the mill yard are tracked based on log stacker events, ensuring that the mill yard inventories are always current. Additionally, online stock analysis provides instant insights into inventory levels, location, and storage time.
4. Lack of Supply Chain Visibility
The wood supply chain is long and complex, often spanning from remote forest locations to processing mills or manufacturers. As wood moves through various stages—harvesting, transportation, storage, and processing—tracking its status and location becomes crucial. Without full visibility, companies risk delays, misplaced inventory, or even having to deal with unexpected disruptions in their supply chain.
The challenge is made worse by the fact that wood products can be stored in different locations, transported via multiple routes, and handled by different partners, each with their own systems and processes. Without a centralized platform for monitoring all these movements, companies are left in the dark about the location or status of their inventory.
Solution
To address the complexities of the wood supply chain, maintaining visibility is key. While tracking the movement of wood through various phases—harvesting, transportation, and processing—can be challenging, focusing on the storage and handling of materials at the mill gate is critical to ensure efficiency. This requires a system that can streamline operations within the yard and prevent disruptions in inventory management. With the right solution in place, companies can optimize storage, reduce handling time, and gain real-time insights into material status, minimizing potential delays or errors.
Managing the transport of wood from forests to production sites can be optimized with LogDrive. By digitizing data chains, LogDrive reduces the risk of manual errors in transport and streamlines logistics, ensuring a more seamless flow of materials from the forest to the mill. It achieves this by facilitating smooth order management, improving stakeholder engagement, and providing better user control.
5. Manual, Excel-Based Workflows
The forestry and logistics industries are not typically known for being early adopters of technology. Many businesses still rely on outdated methods, such as paper records, spreadsheets, or manual processes, to manage their wood operations. This not only leads to inefficiencies but also increases the risk of errors, delays, and missed opportunities for optimization.
Making the switch to modern, digital solutions can be daunting for businesses—especially smaller ones or those with established ways of working. The upfront cost of technology, training requirements, and integration challenges can feel like significant barriers. However, without using technology, businesses risk falling behind competitors who are automating their operations to make their practices more efficient.
Solution
To successfully overcome technological challenges, businesses need to focus on selecting tools that are easy to implement, user-friendly, and scalable. The goal should be to gradually introduce digital solutions that automate manual processes, improve accuracy, and eventually drive cost savings and operational improvements.
YardManager, LogDrive, and BioBiz are all designed with ease of use and scalability in mind. These tools are intuitive, require minimal technical expertise, and are capable of integrating with existing systems. They provide a simple, efficient way to digitize key aspects of wood logistics without overwhelming staff or requiring extensive training.
How Modern Supply Chain Management Solutions Help Overcome Raw Wood Logistics Challenges
The logistics of wood present a unique set of challenges that require smart solutions. Whether it’s rising transportation costs, navigating complex regulations, ensuring efficient storage and handling, improving supply chain visibility, or overcoming technological hurdles, there are significant obstacles to address.
ConiferSoft’s suite of supply chain software, including YardManager, LogDrive, BioBiz, helps businesses overcome these challenges with ease. By implementing these tools, businesses can streamline their operations, reduce costs, stay compliant with regulations, and achieve greater visibility across their supply chain.
With the right technology in place, wood logistics can become a more efficient, sustainable, and profitable operation. ConiferSoft’s solutions provide the infrastructure needed to overcome the logistical hurdles of the industry and set businesses on the path to success.